ACE.
A ONE-STOP MANUFACTURING FORCE.
ACE Clearwater creates custom, complex formed and welded assemblies for the aerospace and power generation industries. As we like to say, “If it flies, we’re on it.” Operating from three facilities within a 10-square-mile radius in Southern California, our employees are the best problem solving team in the business.
ACE is the place for Manufacturing Engineering, Forming, Tube Bending, Welding, Machining, Laser Cutting, Waterjet, CNC Milling & Turning, Tool Design, Assembly and Additive Manufacturing (3D Printing). We have over 250,000 square feet of pure manufacturing agility and people with the experience to make it happen.
ACE is headquartered at 19815 Magellan Drive, in Torrance, CA. Two buildings provide 120,000 square feet of manufacturing space. Housed at headquarters are all administrative personnel, human resources, sales, contracts, manufacturing engineers, planners, program managers and finance. Manufacturing work centers include welding, deburr, water jets, clean line, x-ray inspection, NDT, large and regular format CNC’s, machine shop, spot welding, assembly, shear, tube bending, laser 3D measurement, stores, tooling, quality assurance and final inspection.
Our Paramount facility is located at 14105 Garfield Avenue. Purchased in 1982, Clearwater Tool and Die was added to create the new company, ACE Clearwater. The facility houses one of the largest drop hammer operations in the country, model shop, foundry, spinning, planishing, check & straighten, hand-trimming, shear, and deburr. It also benefits from a complete closed-loop, organic clean line operation and quality team for final inspections, in-house, and adds an additional 140,000 square feet of manufacturing.
Our Compton facility is located at 1614 Kona Drive. In 2002, ACE purchased Honeywell’s metal forming operations, and moved it to the 30,000 square foot building which houses hydroforming, a 400-ton hydraulic press, machine shop and 5-axis laser cutting equipment. It has also been, for four years, the site for ACE MFGDAY celebrations for hundreds of local school children to learn what aerospace manufacturing is all about.
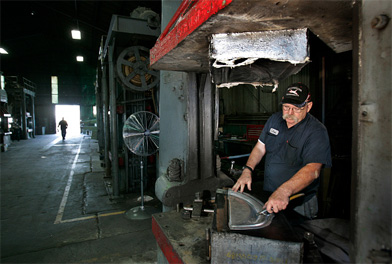
Sometimes old technology still beats the new. Here, one of our metal formers is fine-tuning a formed shape in Drop Hammer Alley, the largest of its kind in the country. Drop Hammers continue to be the best, most controlled and cost-efficient way to transform sheet metal into precision parts.
Embracing the latest in technologies, ACE now also has the highest laser scanning and 3D measurement devices and software available. Along with our additive manufacturing center and its Fortus 3D printers, we set the gold standard for model analysis, quality management and manufacturing control. The fact that ACE, for 55 years, has weathered California’s strict business and environmental laws and regulations –and has, in fact, significantly thrived here – is a testament to our diligence, team strength, hard work and exacting standards.